
Retrofit extraction systems
Retrofit for extraction systems
Retrofitting is when older machines or existing systems are converted or retrofitted. This brings them up to the latest state of the art and can be a sustainable and cost-effective alternative to buying new machine tools or extraction systems.
What are the goals of retrofitting?
Productions have different requirements and processes. Saving costs is a common goal. Outdated extraction systems often consume more electricity and power. The qualitative condition also decreases. Other goals include:
- Avoid downtimes
- Increase product quality and production volume
- Automate production processes
- Increase energy efficiency, reduce energy costs
- Meet legal requirements
- Ensure optimum performance
- Industry 4.0
What are the advantages of retrofitting extraction systems?
Have production processes changed, is more being produced or are there additional jobs? Then the required air volumes and extraction power increase, which it takes to efficiently extract dust, welding fumes or oil mist in a unit. The machinery can be adapted to the new production conditions without a cost-intensive new purchase, which entails further costs such as training of employees, implementation in IT and further infrastructure.
Convert or retrofit?
During converting, obsolete components are replaced. This may concern components for which spare parts are no longer available or there are better alternatives in terms of wear or consumption. This can shorten the maintenance intervals and reduce the costs for wear parts.
If systems receive additional components, this is referred to as retrofitting. Digital and electrical components are often added to increase energy efficiency and automation: control, sensors, communication systems, frequency converters …
Examples of retrofit for an extraction system
Energy consumption, efficiency and extraction power are the trinity in extraction technology. If too much or too little of the contaminated production air is captured and filtered, occupational health and safety and dust limits cannot be met. If the extraction system has more power than is needed, this wastes valuable energy and drives up operating costs. There are several ways to bring extraction power, energy consumption and efficiency up to the state of the art. Thanks to our many years of know-how, we will be happy to advise you individually on the technical possibilities for optimizing and retrofitting your extraction system.
Reasonable retrofittings for exhaust systems:
- Increase energy efficiency and reduce energy costs
- Improve the capture
- Optimization of the pipe system
- Intelligent control
- Remote maintenance
- Automatic power adjustment
- Energy saving through frequency inverter
- Motor replacement for higher extraction power and larger air volumes
- Fire and explosion protection
- Pre-separator attachment
- heat recovery
- Fresh air supply
- and much more
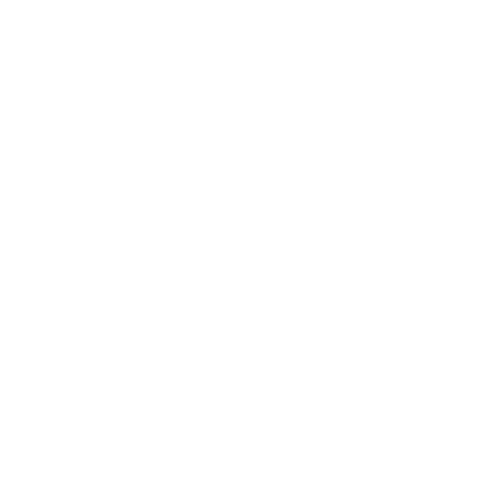
There’s still room for improvement!
Modern control technology on your extraction system brings many advantages. Especially in the energy sector and heat recovery, immense costs can be saved per year! Make your production fit for Industry 4.0 or automate processes for economical and convenient operation, for example with a Siemens LOGO! control.
Intelligent control for extraction systems:
- Frequency converter
- Automatic power adjustment
- heat recovery
- Fresh air supply
- Remote maintenance
- Industry 4.0
FAQs

»Thanks to our many years of know-how in extraction technology, we also maintain and retrofit extraction systems from other manufacturers in a sensible manner. The areas of acquisition, control and piping systems often hide great potential for optimizing and saving your operating costs.«
Martin Prokisch | Technical Manager
Non-binding expert estimate
Do you need our support or would you like individual advice? Please feel free to contact us at +49 731 141 108-0 or use the contact form. We will get back to you as soon as possible.